For simple to complex
conveying paths
Our tube chain conveyors offer a wide range of applications in the optimization and
automation of operational processes for almost all industries. Thereby, we individually adapt
the tube chain conveyor to the complexity and challenges of your conveying path.
11+ industries
2-10 weeks delivery time
500 + projects implemented
up to 80 cbm/h capacity
Advantages
What makes our
Tube Chain Conveyor unique
Our tube chain conveyors are used in 11+ industries with an average 5-6 digit
Return on Investment (€). On four continents, our tube chain conveyors
support over 500 customer projects with 2.6 - 80 cbm/h capacities, meeting any challenge.
Customized
Adapted to your individual conveying routes and conditions.
Gentle
Residue-free discharge, quiet operation, and available in a food-safe version.
Cost reduction
Up to 90% energy savings compared to conventional conveyors.
Fast success
Fast planning and delivery. Installation in a few days to weeks. Return on investment in a few months.
Models
Our product lines
Choose from a range of options to meet your individual needs, from occasional start-stop
operation with little required conveying capacity to high required capacity around the clock.
24/7
designed for demanding operations, with application up to 24 hours 365 days a year.
< 12h / day
designed for normal operation, with application from a few minutes to hours.
We flexibly adapt the model to your industry-specific requirements and wishes.
Components
The main components
of the tube chain conveyor
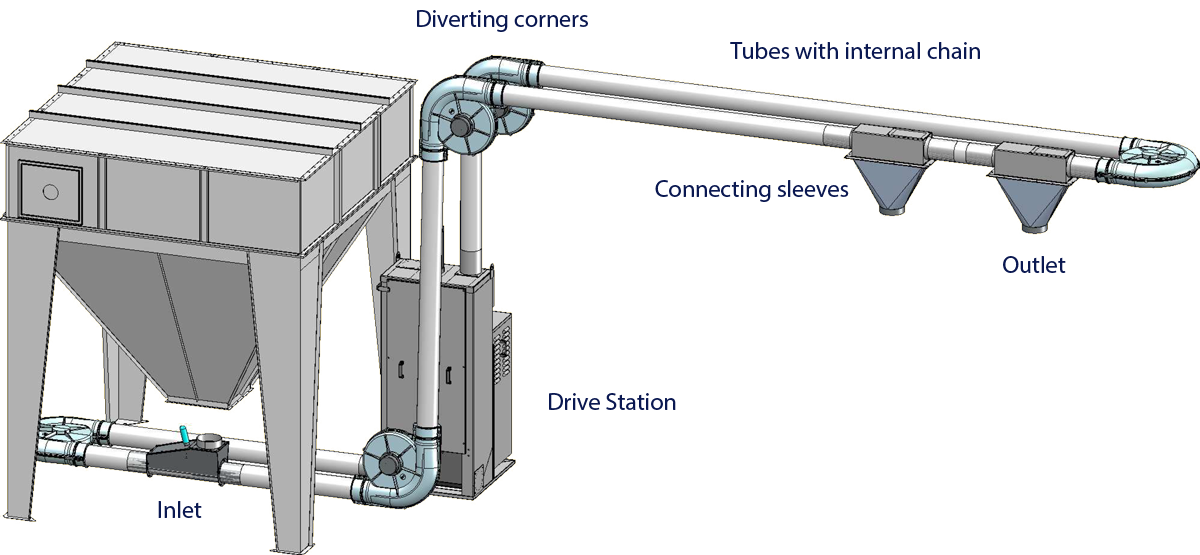

Tubes
Read moreTubes
High quality tubes in which the chain runs, providing support and protection for the materials being transported.
Material
Stainless steel or galvanized steel

Drive Station
Read moreDrive Station
Robust and high quality drive station in different power levels, which moves the chain and is thus the heart of the tube chain conveyor.
Material
Galvanized steel or stainless steel

Chain
Read moreChain
A durable stainless steel chain with carriers that transports the material.
Material
Stainless steel or galvanized steel with nylon carriers.

Diverting corners
Read moreDiverting corners
Strong and durable corners that divert the material flow on the conveyor line by e.g. 90 degrees or 180 degrees.
Material
Stainless steel, cast iron or plastic.

Connecting sleeves
Read moreConnecting sleeves
Stable connection of tubes to allow and maximize the conveying distance.
Material
Stainless steel or galvanized steel

Outlets
Read moreOutlets
Durable outlets that discharge material from the conveyor line. Open, pneumatic or electric available.
Material
Stainless steel or galvanized steel

Inlets
Read moreInlets
Robust inlets that guide material onto the conveyor line. Sizes are variable to suit your requirements. Also available electrically.
Material
Stainless steel or galvanized steel

Others
Read moreOthers
Other components for automating and monitoring your system include full and empty detectors.
FAQs
Questions and answers
We will be happy to answer all your questions about tube chain conveyors in a personal consultation.
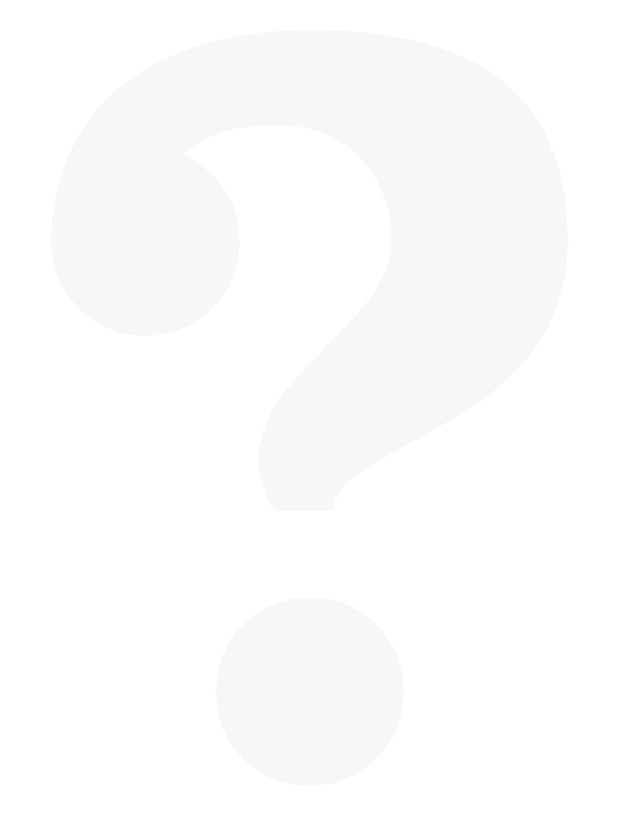